Through a determination not to tolerate defects, this team determined the root cause of recurring turbine generator failures, saving in excess of $500,000 per year and over 128 manhours per generator per year.
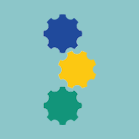
Turbine Generator
Eastman Chemical – Kingsport, TN
By eliminating the defects in their centrifuge equipment, this team reduced their maintenance expenses by $150,000 annually and the additional uptime has added production throughput and $5 million to their bottom line.
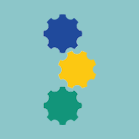
The Centrifuge Team
Eli Lilly – Lafayette, IN
By identifying and eliminating defects in their metering valves, this Action Team reduced downtime on actuators from 6 weeks to a maximum of 2 days.
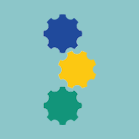
Improving the Odds in the Storeroom
Alyeska Pipeline – Valdez, AK
This action team realized a savings of $5,400 by eliminating a recurring compressor problem.
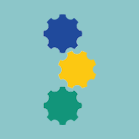
Compressor Bug
Southern Natural Gas – Birmingham, AL
By developing a contingency plan in the event of Feed Tank failure, this action team not only increased crude capacity, it also saved a potential penalty of $2 MM for a 5-day downtime.
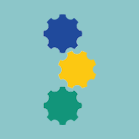
Field Charge Pumps
Gulf Coast Refinery
By identifying defects in their absorber feed pumps, this Action Team eliminated $10,000/episode of purged gas.
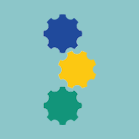
Eliminating Purged Gas
PCS Nitrogen – Trinidad West Indies