Objective: Satisfy customer demand by producing and shipping the finished product without hurting people or the environment, returning a profit to the company.
Roles: Participants gain new perspectives by assuming a different role from the one they perform daily. Maintenance people become operations personnel; business services staff become mechanics; and operators become business services staff. Participants see how their decisions and actions impact each other and the overall performance of the plant.
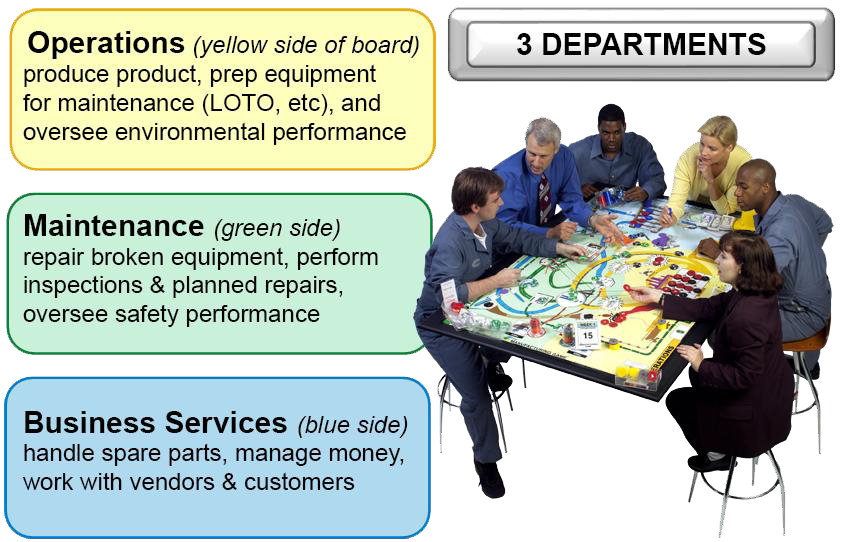